You may have noticed that ATVs do not use alternators to charge their battery as a car do. And you know that keeping the battery topped off is essential for the bike to function correctly.
Many functions like the starter, cooling fans, lights, winch, power steering, heated grips, GPS, and other accessories require electricity.
So how, then, is it being charged? What is generating its juice?
An ATV uses what is called a stator system or magneto system to charge its battery. This is a fairly simple and robust system located on the inside of the ATV’s engine. Any time the engine is running, the stator is continuously generating an electric charge. Some electricity is used to power the bike’s different electrical components. What’s left is being used to charge the battery.
How Does an ATV Stator Charging System Work?
If you’re anything like me, you want to know how your vehicle’s various systems are actually working.
This gives you a better understanding of its capabilities and limitations and makes troubleshooting easier when things do not work as they should.
A stator system can be designed in several ways, but all share the same working principles.
Inside the engine crankcase, you have a shaft (the crankshaft) spinning at the same speed as the bike RPMs. The more throttle you give, the faster this shaft rotates.
The engine power is what powers the charging system. The charging system will “rob” your engine for about 0,5 hp on maximum output, practically making it a non-issue.
Explaining the Stator, Rotor, & Regulator Rectifier
The charging system is connected directly to the crankshaft and consists of three main components. This is a rotor or flywheel, a stator, and a regulator rectifier.

The stator looks like a drum or ring made up of multiple laminated non-conductive bars wrapped in thin copper wire. Each bar works like a coil.
The number of bars varies from manufacturer to manufacturer and model to model, depending on the power output the bike requires. The shaft goes through this ring of coils, but the actual stator does not turn.
One typical charging system style has the rotor mounted directly to the shaft inside the stator. On the outside of the rotor, you’ll have several magnets.
The most common variation, however, is one where the magnets are connected inside a flywheel that spins on the outside of the stator.
Both systems work the same way: When the magnets on the rotor or the flywheel spin past the coils on the stator, the magnet will induce a current in the coils. With each revolution, this current reverses itself, and you get an alternating current.
However, this current is too unstable to be let directly into the bike’s electrical system as the voltage varies in line with the engine speed and, at full speed, is way too high.
The current must also be converted from alternating current (AC) to direct current (DC) before charging the ATV battery. This is achieved by sending the current through a regulator rectifier.
This is usually a compact black or metal box with heat fins to better dispose of the heat the semiconductors create.

The power from this box is ready for use by the rest of the bike’s electrical system.
A common fault on ATVs is when the regulator part of this box fails, and you’ll get too high voltage pumped out into the bike’s electrical system. This may cause bulbs to go out, heated grips to die, and batteries to boil dry.
Measuring your regulator’s output is crucial if you suspect it has gone bad.
Is All the Power Used to Charge the ATV’s Battery?
No, it’s not. A big chunk of the charging system’s power is being used immediately to power the bike’s electric components.
The charging system and the battery are designed to work hand in hand, and the surplus power goes to charging the battery. The battery receives a proper charge when the power draw to keep the ATV running is small.
Other times like when you use a winch, hand warmers, or other power-hungry accessories, you use more power than the charging system can deliver, and energy is taken from the battery.
Why Do ATVs Use Stator Systems and Not Alternators?
Belt-driven automotive-style alternators can create a substantially higher power output than the magneto-style systems used on ATVs. Why do the manufacturers choose an inferior system for our bikes?
Well, it all boils down to technical challenges. An alternator needs a lot of air blown by it to keep it cool. But it has to be relatively dry and clean air. Alternators are not designed to handle the wet and dirty conditions they might encounter on an ATV.
On the other hand, Stator systems are well protected inside the bike’s crankcase and do not require constant airflow to keep them cool as they are designed to tolerate relatively high temperatures.
The combined effect of engine coolant, engine oil, and internal fans keeps the stator system operating within its rated temperature range.
Space limitations are also a deciding factor when the designers use stator systems over alternators, as the latter typically require much more room.
This is no problem in a car’s relatively spacious engine compartment, but on ATVs, the design needs to be compact, which can more easily be achieved with a stator system.
But over the years, ATVs get more and more power-hungry electric components. This puts ever-increasing stress on the bike’s charging system and battery.
To keep up, the engineers have been busy improving stator-type charging systems. The systems have evolved tremendously, and the average power output has increased by 3-4 times from the 1990s until today.
And for the most part, they still manage to keep up with the demand.
Changes that have been made are using a better type of magnets, amping up the number of coils and magnets by increasing the diameter of the flywheel, and moving from a 1-phase to a 3-phase power output system.
Only the future can tell us if ATVs will still be using stator systems for years to come or if the ever-increasing demand for electric power at some point will force the engineers to start looking for alternatives like the alternator or others.
What if the Charging System Cannot Keep Up?
When the bike uses more electricity than the charging system can deliver, the power needs to come from the battery.
ATV batteries have low amp-hour capacities and are primarily meant to power the starter for just some seconds at a time.
Over time, overuse will drain the battery, making you unable to start the bike. And even worse, it can permanently damage the battery.
This can happen when you only use the bike for short periods each time you ride. The starter draws a lot of power from the battery, and the charging system needs some time to charge it back to where it was.
Also, if you do a lot of winching, for example, when plowing, you may use more power than the charging system can deliver. Riding in the low gear range may help compensate for the high current draw, as the higher REVs will give more power from the charging systems.
But sometimes, this is not enough. Then your best option will be to hook up a charger to top off the battery in between each time you ride it.
Related: How to Charge Any ATV or UTV Battery; All You Must Know
I recommend getting a fully automatic battery tender that can be left connected without the risk of overcharging the battery.
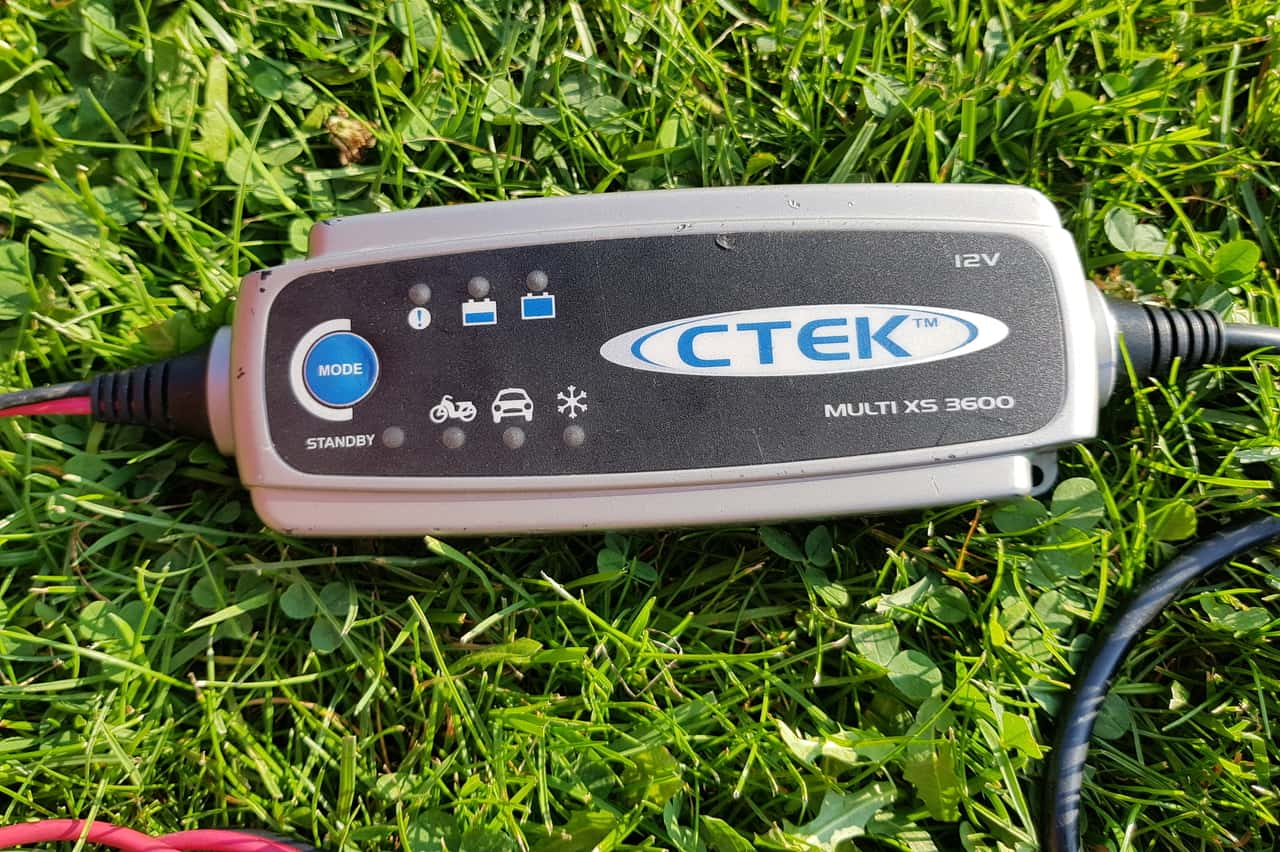
Does It Matter What Battery You Use?
ATVs generally use one of two types of batteries. These are flooded acid-lead batteries (flooded batteries) and Absorbed Glass Mat batteries (AGM).
The acid batteries are the cheapest but cannot handle such a beating that gel batteries can. They are prone to spillage, which is unsuitable for motorsport or off-road applications. Maintaining them can also be quite a hassle.
The AGM batteries are filled with gel and are practically maintenance-free. There is no risk of spillage, and they usually will last a lot longer. They cost a bit more, but the added cost will likely pay off for the average ATV owner in no time.
In my opinion, they are the perfect match for ATVs.
As for charging, the AGM batteries allow for faster recharge and a slower discharge than the flooded acid-lead batteries. This is due to lower internal resistance.